Cooling & Cooling Jackets
Temperatures Inside High-Speed Turbomachinery Have a Serious Impact on System Reliability.
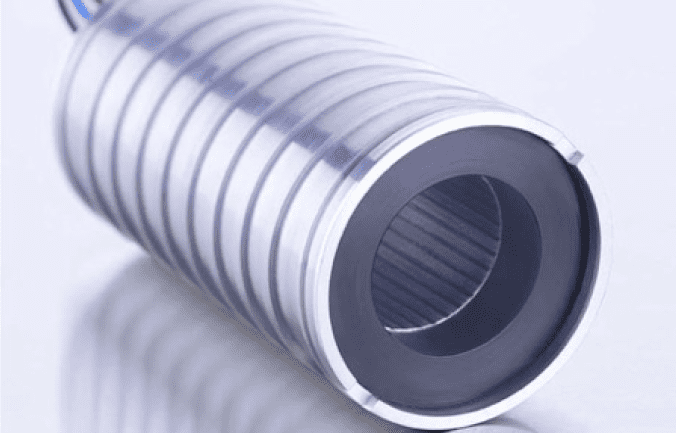
Controlling temperature inside a high-speed motor/generator has the most serious impact on motor life and subsystem reliability than most all other factors. At risk from a temperature perspective inside the motor/generator are basically the slot insulation in the stator and the Permanent Magnets in the rotor.
Aluminum/copper squirrel cage rotors for induction machines can withstand significantly higher temperatures than PM rotors but tip-speed, efficiency and shaft diameter are further tradeoffs in the selection of motor/generator type.
Reliable Turbomachinery is dependent on a robust cooling system.
We build rotor & stator solutions for your application.
Contact us today!
Cooling
-
Cooling Jackets
Motor/Generators can be cooled via direct spray of refrigerant onto the end windings (like in HVAC applications), or air cooling for smaller, lower power motors, but the primary cooling method chosen for most high-speed, high-power applications is liquid cooling using a cooling jacket that surrounds the stator and is then integrated into the customer housing. An example drawing of an e+a cooling jacket is included in the Support and Downloads page and pictures in this section show a rendering of an e+a cooling jacket as well as production stators shrunk into cooling jackets at the factory. The customer is responsible for specifying the cooling system so these cooling jackets can be designed/built by the customer or e+a can provide the cooling jacket with the stator pre-shrunk into it. Cooling jackets are effective with all types of end winding treatments (VPI™, ENCA™ and ALKA™) and e+a nominally specifies the inlet temperature of the fluid to be 27°C. This temperature provides sufficient headroom for heat transfer to occur from the rotor into the stator slots, then through the back iron and into the cooling jacket. Higher liquid inlet temperatures will result in higher rotor and stator temperatures. Maximum target stator internal temperature for Class F insulation systems is 155°C; for Class H systems, 180°C.
-
Permanent Magnets
Temperature limits on Permanent Magnets vary significantly, but on average most Permanent Magnets will demagnetize completely when the magnet temperature reaches approximately 220°C, so e+a recommends that the rotor temperature of Class F systems be held to no more than 155°C and Class H systems be held to no more than 180°C. This provides some headroom on the temperature profile and also takes into account the fact that the carbon fiber sleeve is somewhat of an insulator so the magnets heat up more when using a carbon fiber retaining sleeve instead of a steel sleeve (MEBA™).
-
Slot Insulation
e+a provides motors with two classes of slot insulation: Class F, good up to 155°C, and Class H, good to 180°C. To get a perspective on how temperature can affect system reliability, if the internal temperature of the inside diameter of a Class H stator is kept at 180°C, then the life of the insulation in the stator will be approximately 10,000 hours. For each 10° C of temperature below 180°C, the lifetime of the stator is doubled. So for example, if the stator ID of a Class H stator is kept at 150°C, then the stator life will be approximately 80,000 hrs.